When it comes to workplace safety, your feet might not be the first thing on your mind, but they certainly should be. Wearing the right footwear can mean the difference between walking away from a mishap and facing serious injury. That's where OSHA approved footwear comes into play, setting the standard for protective shoes in work environments.
But how do you know what qualifies as OSHA approved? And why is it so important? Industries ranging from construction to manufacturing have unique risks that make selecting proper footwear crucial for all employees. Understanding these footwear standards can not only help ensure compliance with regulations but also promote a safer, more comfortable work experience.
Let's delve into what makes footwear OSHA approved, the specific features to look for, and tips to help you choose the best pair for your workplace needs. Your safety from the ground up starts here!
- Introduction to OSHA Footwear Standards
- Common Workplace Hazards
- Features of OSHA Approved Footwear
- Choosing the Right OSHA Footwear
- Maintenance and Care Tips
- Cost versus Safety Trade-offs
Introduction to OSHA Footwear Standards
In the hustle and bustle of today’s industrious world, from towering skyscrapers to quiet office spaces, ensuring a safe work environment is pivotal. The Occupational Safety and Health Administration, known by its acronym OSHA, plays a vital role in setting standards to protect workers from various professional hazards. The focus on footwear within these regulations emphasizes the importance of protecting the often-overlooked foundation of our body – the feet. OSHA has crafted guidelines to help ensure that work shoes are not only comfortable but also act as a shield against potential hazards.
These OSHA footwear standards aren’t arbitrary checklists but are based on rigorous science and evidence from the countless industries they cover. The rules require that safety footwear meet specific criteria defined under the ASTM (American Society for Testing and Materials) standards. These include aspects like impact resistance, compression resistance, and the ability to guard against electrical hazards. However, what sets OSHA apart is its commitment to evolving these guidelines to meet the ever-changing demands of modern workplaces, ensuring that risk factors are adequately addressed before accidents occur.
Why OSHA Standards Matter
Understanding the importance of these standards is essential for both employees and employers. A significant portion of workplace injuries can be attributed to foot injuries, a fact that OSHA clearly accounts for within their documentation. Slipping on a factory floor, stepping on a sharp object, or even injury from a rolling object are realities faced by many workers. Without proper protection, an employee could face weeks or even months away from work due to an incident that might have been preventable. It is reported that about 25% of all disability applications are related to injuries to feet and ankles, illustrating the impact these incidents have on both personal and professional levels.
"Safety doesn't happen by accident. It's a culture, nurtured over time." - Anonymous Industrial Safety Expert
Key Features of OSHA Approved Footwear
There are several hallmark features to look for in OSHA approved footwear. From a durable construction that withstands impacts to slip-resistant soles that grip the smoothest floors, each element plays a role in safeguarding the worker. The selection process from OSHA involves rigorous testing to ensure footwear not only protects but also increases efficiency by providing comfort across long working hours. Protective toes, puncture-resistant plates, and insulated soles for electrical protection are just some of the features these safety footwear options boast. When selecting a pair, it’s vital to ensure they match OSHA’s guidelines, which can be referenced in detail under CFR (Code of Federal Regulations) 1910.136, a treasure trove of information for anyone serious about safety.
Common Workplace Hazards
The workplace can be an obstacle course of unseen hazards, all of which can be mitigated with the right preparation and equipment. Footwear, while often overlooked, plays an essential role in shielding workers from a variety of threats. One of the most prevalent hazards is the risk of falling objects, particularly in environments like construction sites or warehouses where tools and materials are frequently moved overhead. Dropped tools or goods can cause severe injuries to the feet. The right pair of OSHA footwear can provide reinforced protection to prevent such injuries, often by using a steel or composite toe cap.
Slip and trip hazards are another danger lurking in many workplaces. Slips can occur when there is oil, grease, water, or other substances on the floor, which may lead to anything from minor bruises to serious fractures. Proper work shoes come with non-slip soles designed to enhance grip and prevent these incidents, reducing workplace injuries remarkably. According to the National Safety Council, the average workplace sees about 25% of all injuries resulting from slips and trips, highlighting the need for specialized safety footwear.
Puncture hazards, while less of a household name, pose a significant threat to those working in areas with sharp objects. Stepping on nails, shards of metal, or other pointed debris can lead to nasty lacerations or infections. For individuals in construction or manufacturing, shoes with puncture-resistant soles are not just recommended but considered essential. To put it into perspective, many regulations even mandate the use of such protective shoe features. “Safety isn’t expensive, it’s priceless,” emphasizes Jerry Smith, a noted safety consultant, capturing the essence of why investing in protective footwear matters.
Electrical hazards take priority in environments where workers are exposed to circuits, wiring, or static electricity. Electrical shocks can be abrupt and potentially fatal, making it crucial for those in such fields to sport electrically safe footwear. Specialized rubber-soled shoes can insulate and protect against unintended shocks. According to a study by the U.S. Bureau of Labor Statistics, electrical burns and shocks constitute a considerable portion of workplace accidents among electricians, underscoring the need for compliance with safety footwear that caters to electrical resistance.
Chemical spills can also pose grave threats in settings like laboratories or factories where hazardous materials are present. Corrosive substances can damage regular shoes, leading to skin burns or absorption of toxic materials. Footwear that offers chemical resistance is vital in protecting workers from these potential dangers. It is essential for employers to consider each of these hazards carefully and equip their teams with the relevant protective footwear. Understanding these hazards allows businesses to tailor their safety measures effectively, not just meeting OSHA regulations, but ensuring every step taken by a worker is a step towards safety.
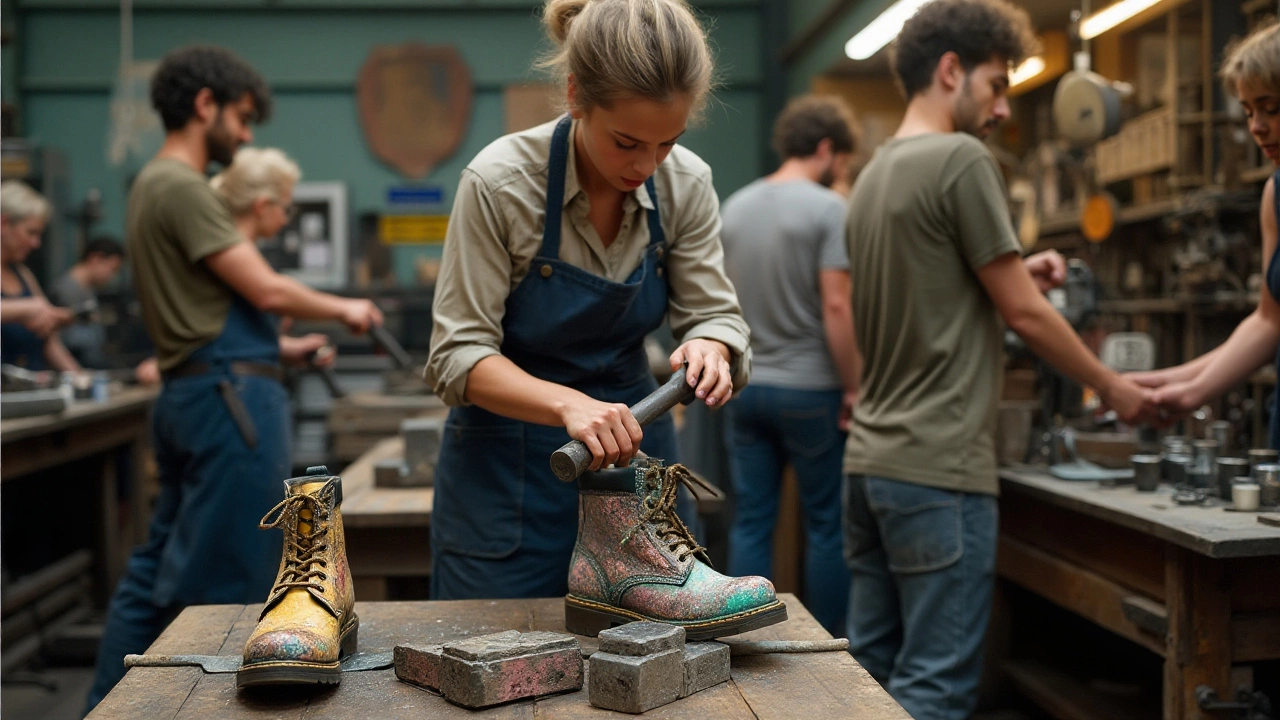
Features of OSHA Approved Footwear
When considering workplace safety, the focus often shifts to helmets and gloves, but it's imperative to give equal attention to what's on your feet. OSHA approved footwear is meticulously designed to safeguard workers from various occupational hazards. To meet OSHA's stringent criteria, these boots and shoes incorporate multiple protective features that adapt to diverse environments. Firstly, the presence of a reinforced toe area, typically made from steel, aluminum, or composite materials, is a hallmark feature. This toe cap is crucial in preventing injuries from falling objects or compression hazards. Its strength and resilience are recognized across industries as a first line of defense for those working in physically demanding situations.
The soles of OSHA approved work shoes must be slip-resistant and durable, providing grip and stability on various surfaces. Whether dealing with oil-slicked floors or uneven terrain, these shoes help prevent slips and falls, which cause numerous workplace injuries annually. Some soles employ advanced technologies incorporating rubber compounds specifically engineered for increased traction. Such safety features are critical in industries like manufacturing and construction, where workers frequently navigate potentially treacherous surfaces. Equally important is the electrical hazard protection. Certain OSHA approved footwear is designed to resist electrical shocks, keeping the wearer safe from currents in environments with live wires or other electrical risks.
Beyond these vital protective features, comfort plays a significant role in the design of OSHA compliant footwear. Ergonomic fit, breathable materials, and cushioned insoles come together to ensure that workers not only stay safe but also maintain productivity and movement ease. The shoes are often tailored to accommodate long hours of wear without causing fatigue. Indeed, the daily rigors of a demanding profession necessitate footwear that can keep pace with worker needs without compromising on armor or comfort.
According to a study by the National Safety Council, proper safety footwear can reduce workplace injuries by up to 80%. This statistic is a testament to the significant difference such footwear makes in ensuring safety and preventing costly incidents. Understanding these features allows workers and employers alike to select the most appropriate footwear, tailored to the specific risks present in their work environment. In the words of one prominent safety expert, "The foundation of workplace safety starts from the ground up, in each step you take."
Choosing the Right OSHA Footwear
Deciding on the perfect pair of work shoes that meet OSHA standards can feel like a daunting task, especially with so many options available today. The journey to finding the right OSHA footwear should start with identifying the specific hazards present in your workplace. Whether you face risks from electrical exposure, slippery surfaces, heavy objects, or sharp materials, it's essential to understand the exact dangers you're protecting yourself from. Equally important is considering the type of work you do—are you constantly on your feet? Do you work outdoors or indoors? Each of these factors can influence the kind of protection and comfort needed in your safety footwear.
A key component in selecting OSHA approved footwear is the style and material. Steel-toed boots are great for protecting against heavy objects, while composite toe shoes offer a lighter, often more comfortable alternative without compromising protection. For those dealing with oil or water, slip-resistant soles are a must. Electrical hazard-rated shoes are crucial for environments with electrical risks. These choices don’t just emphasize safety—they enhance comfort, ensuring you don't suffer from sore feet after a long workday. A survey by the National Safety Council found that foot injuries constitute nearly 25% of all workplace injuries, underscoring the importance of proper footwear.
It's also worthwhile to explore how the shoes are constructed and how durable they are under wear and tear. Echoing expert opinions,
"It's not just about safety features, but how the shoe supports your daily needs and lifetime of use," suggests footwear expert John Smith from the American Society of Safety Engineers.Many manufacturers now also incorporate athletic or casual designs into their protective shoes to appeal to workers' personal style, making them not only functional but also visually appealing.
When shopping for the right pair, trying on different shoes and paying attention to fit and comfort is essential. Consider doing this in the afternoon, as feet tend to swell throughout the day. This ensures you account for any size changes as your feet experience long hours on the job. Additionally, invest in brands recognized for quality and adherence to safety standards. Reading reviews and seeking recommendations from colleagues can also provide insights into the durability and comfort of specific models.
Don’t overlook the importance of regular inspection and replacement of your work footwear. Worn soles, damaged safety toes, and compromised materials indicate it's time for a new pair, as these issues can undermine the protective features the shoes offer. According to a study by the Occupational Safety and Health Administration, regular replacement intervals vary, but most experts recommend evaluating footwear every 6 to 12 months, depending on wear intensity and environmental conditions.
Creating a balance between cost and safety is crucial. While it might be tempting to opt for lower-priced shoes, especially when buying in bulk for a workforce, always consider the broader implications for safety and productivity. A slight increase in expenditure on your OSHA footwear can lead to a decrease in workplace accidents, contributing to a safer, more efficient work environment. Remember that the investment in quality safety shoes is an investment in well-being and, ultimately, peace of mind on the job.

Maintenance and Care Tips
When investing in OSHA footwear, it's not just about making the right purchase; maintaining and caring for your work shoes is equally crucial. Proper maintenance ensures longevity, sustains protective features, and guarantees comfort. Begin with regular cleaning to remove dirt and grime that accumulate during work. Use a soft brush or cloth to wipe the surface gently, followed by a mild soap if necessary. It's essential to check your shoes after each use, paying attention to any visible wear and tear. Keeping them clean and in good shape not only extends their lifespan but also ensures they continue to meet safety requirements.
Another key aspect of maintenance is conditioning leather shoes regularly. Leather is a popular choice for work shoes because of its durability and comfort, but it can become hard and less flexible over time. Applying a leather conditioner helps in keeping the material supple and prevents cracks. Take care when applying conditioners, using an appropriate amount to ensure even coverage without buildup. For shoes featuring synthetic materials, a simple wipe-off with a damp cloth followed by a dry cloth is sufficient to maintain their integrity.
“Taking care of your safety footwear should be a daily routine. It's an investment in not just the shoes but your safety at work.” - Mark Sullivan, Safety Expert.
The next step in effectively maintaining your safety footwear is seizing the opportunity to inspect the soles. Pay attention to the tread pattern; good traction is critical for slip resistance, and worn treads can increase the risk of accidents. If the soles are showing signs of severe wear, it might be time to replace them or the entire shoe. Many brands provide re-soling options, which can be an economical solution compared to buying new pairs.
Storing your protective shoes properly is also extremely beneficial. Ideally, store them in a cool and dry location to prevent moisture buildup that can lead to odors and deterioration. Ensure shoes are not kept in direct sunlight, as excessive sunlight exposure can damage material and adversely affect the shoe's fit. Using shoe trees can help maintain the shape and aid in drying out any moisture accumulated during the day. This proactive strategy keeps the footwear in form and prevents premature wear.
Lastly, it's imperative to let your work shoes breathe. Rotating between multiple pairs, if feasible, allows each pair to air out and reduce odor formation and bacterial growth. This practice not only extends the life of each pair but also contributes to improved hygiene and comfort, especially in robust work environments. Ultimately, by following these practical tips, you can ensure your protective shoes continue to do their job, keeping your feet safe and secure, job after job.
Cost versus Safety Trade-offs
When it comes to OSHA footwear, one of the most pressing considerations employees and employers face is the balance between cost and safety. Investing in quality footwear is essential, but it's no secret that these shoes can come at a higher price point. However, let's consider the math beyond the initial cost. The figures reveal that the upfront investment often pays dividends in longevity and protection. For instance, a solid pair of safety boots made from rugged leather with reinforced toes might set you back more initially, yet they boast a lifespan significantly longer than their cheaper counterparts. That longevity translates to less frequent replacements and ultimately, savings over time.
To put it simply, saving money by opting for less expensive, non-compliant shoes is a risk that could result in costly consequences. Workplace injuries, after all, are not only physically harmful but economically draining. Consider this sobering statistic: according to the National Safety Council, the median cost of workplace injury compensation claims is over $40,000. It's worth noting that feet injuries, which could be alleviated by proper work shoes, account for numerous claims every year. From this perspective, the price of quality safety gear is dwarfed by the potential expenses of medical bills and lost productivity.
There’s also a comfort element to this trade-off. High-quality safety footwear not only protects but can also improve the day-to-day comfort of workers. Many advanced models incorporate ergonomic designs, cushioned insoles, and breathable materials. This is not just a perk—comfortable workers are often more productive and report higher job satisfaction. In essence, the choice of footwear can influence workers' overall effectiveness and morale, which in turn benefits the bottom line.
In a
2022 report from the Occupational Health and Safety Administration, it was highlighted that “investing in the right safety equipment, including footwear, can reduce the incidence of workplace injuries significantly.” This underscores the notion that while the initial expense might seem daunting, the return on investment is realized through enhanced worker protection and performance.
Deciding between cost and safety means recognizing these expenditures as investments in your workforce's wellbeing. When considering footwear options, look for independent quality assurances like ASTM and ANSI ratings to ensure compliance and durability. It's a balance, yet one skewed definitively toward delivering the best protection for those who spend long hours on their feet in potentially dangerous settings.
It’s clear that by prioritizing proper footwear in the workplace, companies are proactively safeguarding their workforce and elevating operational efficiency. Whether it's protective shoes against electrical hazards or protective features like slip-resistant soles, the blend of safety and cost-efficiency is achievable. Employers should consider establishing footwear procurement programs that guide employees in making informed choices, ultimately securing both their safety and financial prudence.